More than 10 Makin’ 3D systems are used on the Skanska refurbishment project of the hydroelectric dams in Trollheimen in Norway.
The dams serve as reservoirs for Gråsjø and Trollheim hydroelectric power plants in the Surnadal and Rindal municipalities in Norway. The energy production provides electricity to 50,000 households. The dams need to be refurbished and upgraded to meet modern-day standards.
Climate change requires higher protection of Norway’s dams
In addition to power generation, the dams also make a significant contribution to flood control in the watercourse.
Dam safety is extremely important. Without stringent safety measures, a dam breach could, in the worst case, wash away an entire town. The Follsjø and Gråsjø dams have been built to the highest safety class, Class 4, according to the Norwegian Water Resources and Energy Directorate (NVE), which sets strict requirements for the construction of the dam. The dams need to be reinforced and prepared for accidents and increased precipitation due to climate change in the future.
The work consists of lining the dam sides and tops of both dams with new and larger stone blocks. These stone blocks are extracted from a quarry established near the flood channel for the Gråsjø dam. In addition to dam lining, also called rock batter, the upper spillway gate will be replaced to increase the capacity of the flood runoff system at the Follsjø dam. New leakage monitoring systems will also be established on both dams.
– The quantity of stone we need to produce is approximately 500,000 cubic meters for incorporation into the three dams, and there are about 4,000 cubic meters of concrete that we need to use on the project, says Thomas Fjeld, Project Manager at Skanska.
High precision is needed for work of this kind which involves lining the dams with an intricate layer of stone blocks on both sides and on top of the dams.
The rock barrier or rock batter is built with the technique called rock ripraps that involves the use of large, durable rocks or stones to prevent erosion, stabilize embankment, and prevent soil or sediment displacement due to the forces of water.
The riprap technique involves the use of rocks or stones that are typically angular or irregularly shaped. These rocks are selected for their durability and ability to withstand the erosive forces of water. Even the color of the rocks is important for aesthetic reasons. The rocks are elaborately placed to form a protective barrier. Excavators interlock the rocks to prevent them from being easily dislodged by the flow of water.

Left: Wood constructions were used to ensure the desired angle of the rock batter. (Source: Gol bygdearkiv) Right: Today, machine control is used to ensure the correct angle of the rock batter as well as the compaction and measuring of the height of each individual rock.
– We use machine control when we construct the dams. Each machine has a GPS system, and there are very strict accuracy requirements in terms of how stones are placed in the dam sides, says Thomas.
The height and location of each single stone are measured directly by the machine operator. The excavator operator places the bucket on top of the stone and measures the height directly in the machine control software.
– It’s like a puzzle. Each individual stone has the exact same requirements in terms of its positioning with respect to the geometry, so it’s important that the machine control works throughout the process to ensure the correct alignment of the entire dam.
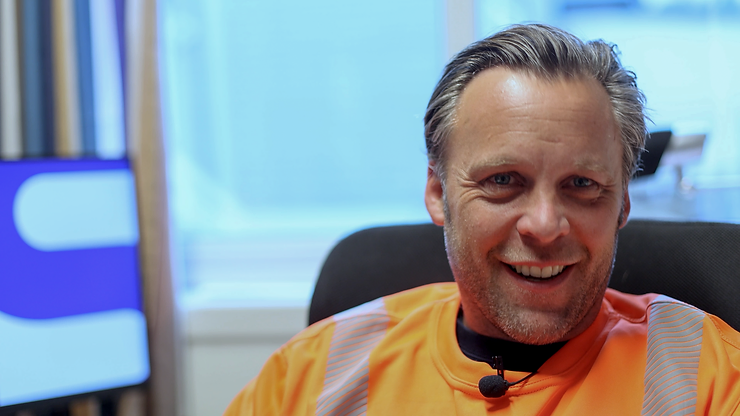
Thomas Fjeld is the Project Manager for Skanska at the Trollheim dam project.
Makin’ 3D solutions work seamlessly together
10 Makin’ 3D solutions are used on the project consisting of 8 Makin’ 3D Excavator solutions on Skanska’s own excavators and on rented machines. The foremen and surveying engineers use the Makin’ Survey which is Makin’s rover solution built on the same platform as the Makin’ 3D Excavator solutions. Makin’ Survey solutions are used on the project by Skanska’s employees as well as by employees from Statkraft. the Norwegian state-owned company Statkraft is the contractor on the project. The Statkraft Group is Europe’s largest producer of hydropower in Europe.
The foremen use the Makin’ Survey solutions for grade checking, creating smaller models, extending the design, and staking out lines. Makin’ Survey is built on the same software platform as the other Makin’ solutions, and all measured points are shared in real-time in Makin’ Cloud.
– Makin is very user-friendly. We can follow all the elements we need to build and simply make changes in the system as we go along. It’s a great advantage that it’s easy for those operating the machine to follow what needs to be built, says Thomas.
The calibration of the machine control is checked every day to ensure that the accuracy is correct.
– The operators in the machines are very satisfied with Makin. They think that it is a system that is easy to understand and simple to use, says Thomas.
Author and photographer: Karina Lykke Lumholt