Flemming Pedersen, trackmaster at the privately-owned railway company Lokaltog, purchased a Makin’ 3D machine control system together with a Makin’ Survey rover solution for machine guidance and as-built documentation. The idea of using the system for the localization of track errors has further optimized efficiency during night maintenance work.
Flemming Pedersen serves as the trackmaster at Lokaltog A/S, a private railway company. With a workforce of around 520 employees, Lokaltog is responsible for managing and maintaining approximately 500 km of railway tracks, as well as operating trains and various buildings owned by the company.
Lokaltog is embarking on a new project focused on renovating the eastern section of their railway network. As part of this endeavor, the company has made the decision to acquire a Makin’ 3D Excavator and Makin’ Survey systems. These systems will be utilized for constructing and measuring railway ditches.
Atkins A/S, a world-leading design, engineering and project management consultancy company, has designed the ditch profiles used in the Makin’ 3D system for excavating the ditches. These ditches are constructed with carefully calculated slopes, as well as design models for the railway tracks, which also feature slopes and underpasses, among other elements.
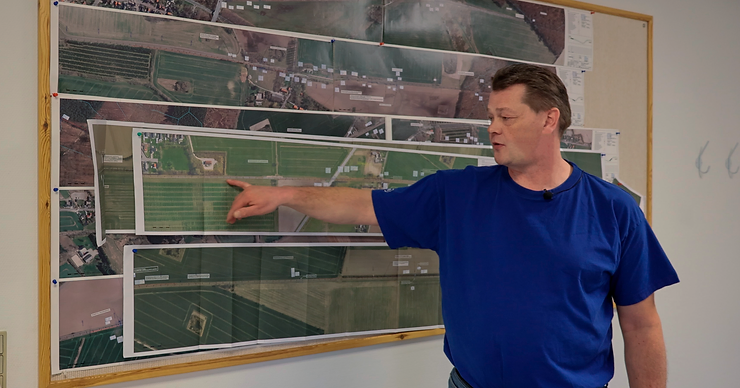
Flemming Pedersen shows the models for the renovation of the eastern part of the railway.
Fostas rents the excavators with machine control
Niels Bundsgaard is employed as an excavator operator at Forstas A/S. He operates the unique rail excavator provided by Hydrema that is equipped with the Makin’ 3D system.
– We at Forstas have rented the machine from Lokaltog because it has the machine control system, says Niels.
He utilizes the excavator to dig new ditches and shape railway track profiles. Taking the lead position ahead of two other excavators, Niels leverages the Makin’ 3D system to establish reference points, which guide the excavation work performed by the other machines.
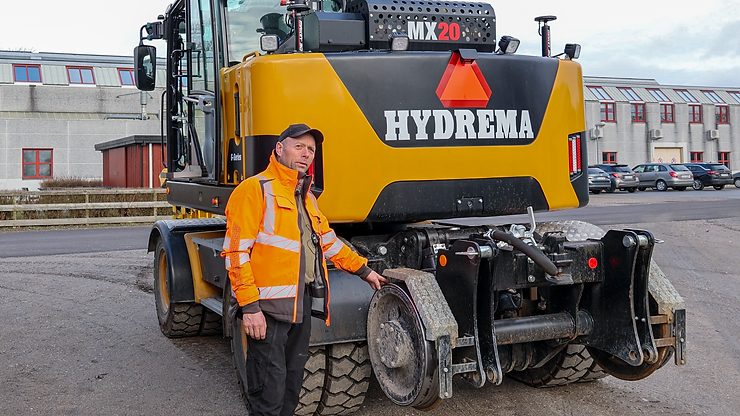
Niels Bundsgaard in front of the Hydrema wheeled excavator specially designed to run on railway tracks, which is now equipped with a Makin’ 3D machine control system.
Getting more use out of the Makin’ 3D system
In addition to using the machine control system for guidance during the excavation of new railway ditches and the cleanup of existing ones, Lokaltog employs it for as-built documentation purposes. This involves documenting the precise positions of various elements such as wells, level crossing detonators, cables, sleeves, and more.
Twice a year, a track inspection vehicle conducts thorough inspections of the railway tracks. During these inspections, any track errors are identified, necessitating maintenance work. Among these errors are the Class 4 errors, which pertain to safety issues like incorrect track height or width. The track inspection vehicle measures the position and category of these errors, and the GNSS data is now directly imported into the Makin’ 3D system utilized in the excavator to rectify these errors.
– I came up with this idea, because I thought that it would be smart to use the Makin’ 3D system for more than just excavation guidance, says Flemming.
The points marked as a Class 4 error can be shown directly on the Makin’ tablet inside the cabin and show the distance to the next error directly.
– Now, we don’t have to use Google to find the position of the points, so we can work continuously without searching for them, explains Flemming.
This has saved Lokaltog a lot of time. Maintenance is done at night, so it could also be difficult to find the points in the dark.
According to Flemming’s estimation, Lokaltog can now effectively address an additional 3 to 4 errors per night by directly incorporating the Class 4 errors into the Makin’ 3D system.
Author and photographer: Karina Lykke Lumholt