We meet Stefan Lindby and his son Hugo on a sunny autumn day in November. They are the owners of the construction company “Väg och Byggnadsgrus på Gotland AB” located on the Swedish island in the Baltic sea Gotland. They have taken the boat to the mainland to pick up a new excavator. The family-owned company was founded by grandfather Gösta and is now run by third generation. Business is doing well, and about seven months ago, they decided to make the biggest investment in the history of the company. They decided to buy no less than 18 Makin’ 3D machine control systems, not only to increase productivity but also to improve the overall profitability of the company.
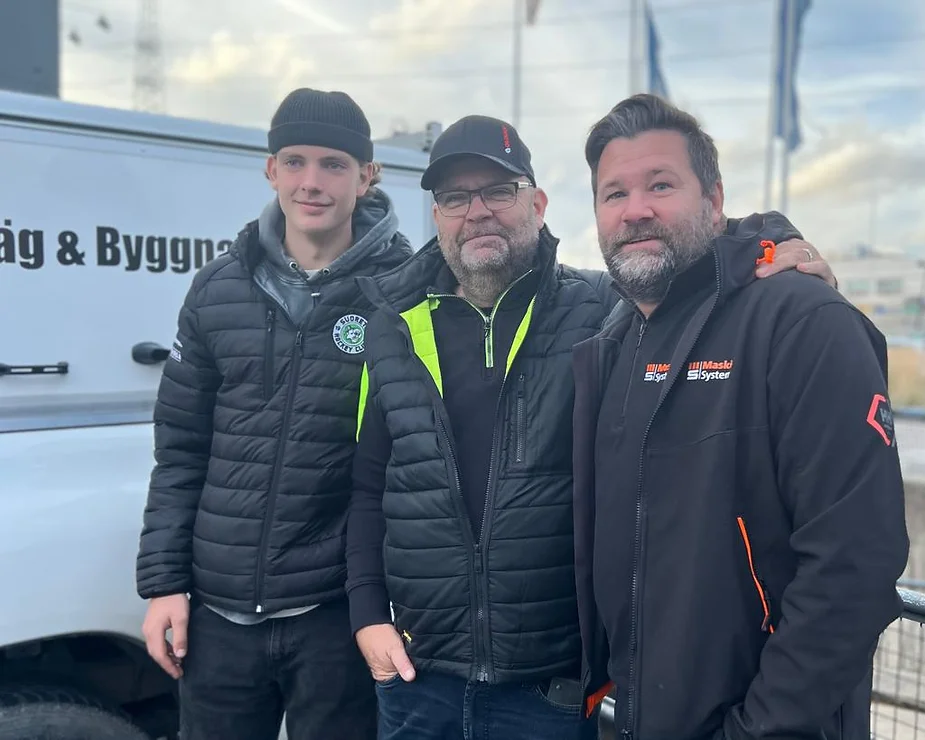
Hugo with Stefan and Andreas from Maskin System.
Makin’ 3D is a more modern machine control system with easy project flows throughout the entire workflow
They had considered the change of machine control systems for a while. Their existing systems were starting to get outdated resulting in more and more repairs and costly downtime. They had bought a machine that already had a Makin’ system installed. They didn’t know the system and called Maskin System’s support to get help to get started. They soon realized that Makin’ 3D is a more modern machine control system with easy project flows throughout the entire workflow.
Stefan decided to compare the different suppliers on the market and was curious about the functions and advantages that were available.
– We thoroughly evaluated the system that we needed, and we explored the functions that were available and how they could help us, Stefan explains.
The decision was not easy. Many hours were used for discussions, tests and evaluations. They also knew that they needed a supplier that they could trust and count on for good cooperation in many years to come. The choice was finally made. They chose Maskin System and their system Makin’ 3D.
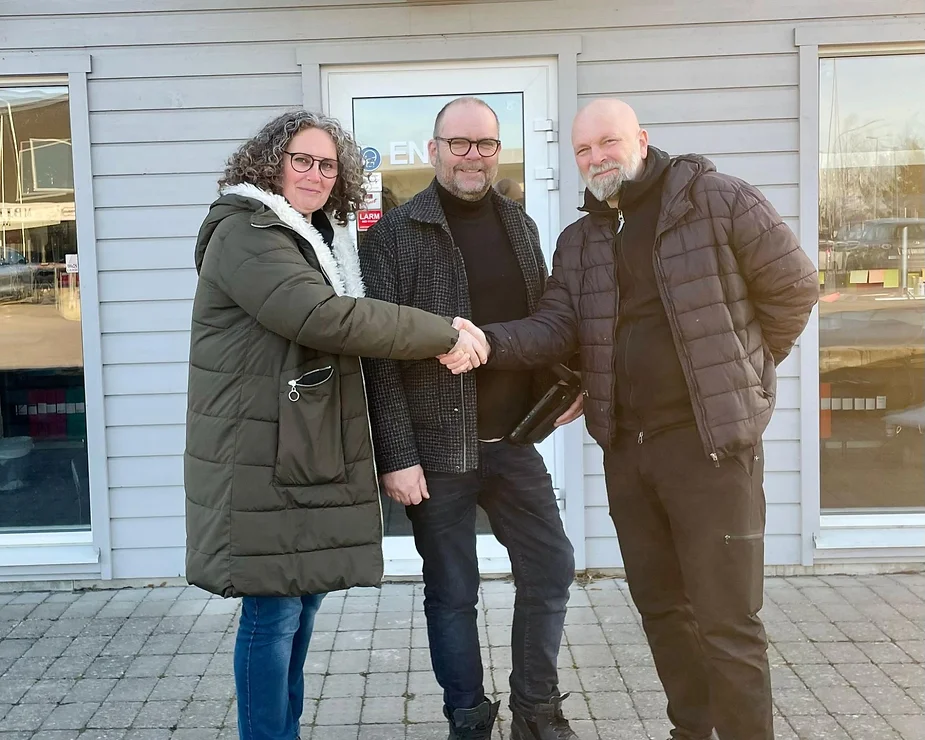
Lotta and Stefan shake hands with Simon Skinnars from Maskin System AB.
– The most positive thing is that all of our machine operators understand it but also that our office personnel have access to all the project information. Everything is updated in real time, everybody is informed and the workflow is much more seamless.
When it comes to hardware, explains Stefan, what is most remarkable is the extremely strong performance of the GNSS receiver. It works flawlessly even inside the forest, where others normally block. This has been a key factor, because all of our machines are running 3D with GNSS.
Delivering 18 machine control systems to a company on an island was a rock’n’roll experience
Gotland is an island, as we all know, and everybody within our industry understands that it can be quite a hassle to deliver and install an entire 18 systems. But Maskin System managed to do just that in record time! Four technicians delivered 16 systems in four days, and the remaining two systems were delivered shortly after. Stefan describes it as an amazing rock’n’roll experience.
– It took some long working days and many visits to McDonald’s Drive Thru, but it was quite a fun experience for both parties.
When we asked Stefan if he had reservations about choosing Makin’ 3D, he paused for a while and then explained that there was some concern about making one of the company’s biggest investments in a relatively new machine control system, and not knowing the exact second hand value.
– Makin’ 3D is developed in Scandinavia and has been on the market for fewer years compared to other suppliers that are “worldwide”, so it is easier to calculate.
But only time will tell, and Stefan is not concerned.
Makin’ Surfaces will bring even more value to Makin’ 3D
– We strongly believe in Makin, and we see them take a larger and larger market share and show strong growth rates. With the upcoming release of Makin’ Surfaces, which is a solution that automatically calculates volumes, the future looks even brighter.
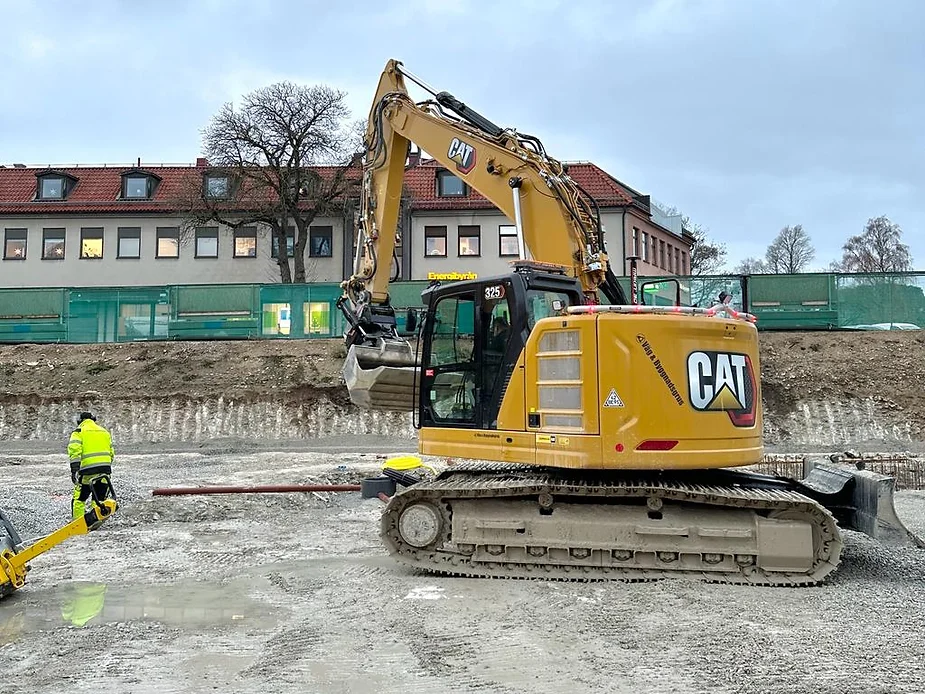
Calculating volumes is a very important part of any construction project.
A large part of the project is about calculating volumes. Stefan explains that it will become increasingly important because surveyors spend about 10 to 12 hours per project measuring mass volumes. Automation of this function directly in the system can bring important savings, and the efficiency in the project can be increased.
– We are also helped by the fact that during the seven months that we have used Makin’ 3D, we have only required service once for one cable and one sensor. That has by far exceeded my expectations, says Stefan.
As a boy Stefan spent all of his spare time on the farm, and he recalls his first job as a little boy. It involved collecting snow poles, and it was very important, according to his grandfather, that there were 25 snow poles in each bundle. The interest for machines and the company grew each year and in 1990, the first excavator was purchased, and the earthmoving part of the business started developing. This was the time when Stefan entered the company alongside grandpa Gösta.
Väg och Byggnadsgrus på Gotland AB is specialized in earthmoving and construction and is continuously expanding their machine park. The company employs about 50 people and all of Stefan’s family is working in the company, including Stefan’s wife, Lotta and their four children: Gustav, André, Tom, and Hugo. When we ask the youngest son, Hugo, which of the machines is the coolest to drive, he answers without hesitation: the excavator, of course!
Stefan is first and foremost thanking their customers:
Stefan seems so interested in his work, and we dare to ask Stefan if he has any free time at all. Stefan laughs whole-heartedly.
– I am blessed with four grandchildren that I want to spend as much time with as I can. Small moments when for example the three-year old Nils joins me in the workshop and helps me fix my vintage cars are just amazing. My wife and I have one of those mobile homes that we sometimes dream about driving away in for a week a year. But quality time for me is to spend my days together with my family and sometimes go for a ride.
We are approaching the end of our interview with Stefan, and we thank him for letting us get to know him and his company. We are of course very proud and happy that they chose Maskin ystem and Makin’ 3D and of the success it has brought to the company.
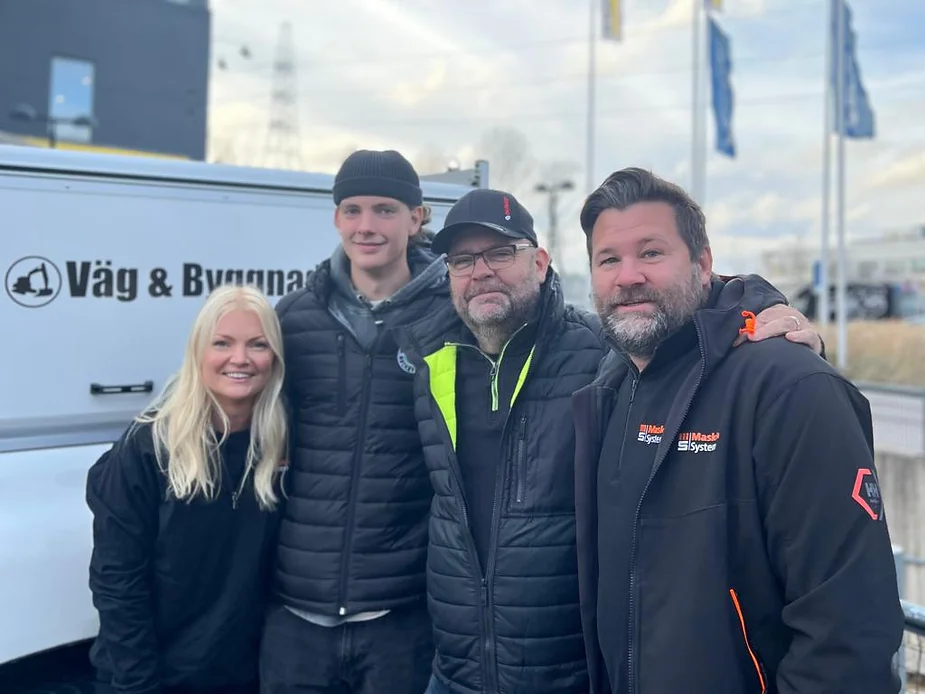
Hugo and his dad Stefan flanked by Andreas and Wenche from Maskin System AB.